Product Inspection of Stainless Steel Reducers
Inspection of Stainless Steel Reducers
1. Geometry analyses of stainless steel reducers
The distribution trends of wall thickness of big and small concentric reducers are exactly the same. From the large end face to the section close to the small end face, the wall thickness changes from thin thickness to thick one. The inner hole of the small end has been turned after forming, and part of the wall thickness has been removed. However, the wall thickness of end faces of small ends is thinner than that of end faces of large ends, which is exactly the opposite of the eccentric reducer. This is caused by the manufacturing process. When the wall thickness of the axial section changes, there is obvious regularity for changes between the warp threads, but there is also a certain degree of dispersion.
2. Analyses of strength
The distribution trends of surface hardness of the large and small eccentric reducers are roughly the same, but they are not completely the same. The main difference is the hardness of the small end. The hardness of the small end of small eccentric reducers is higher, while the hardness of that of large eccentric reducers is lower. The tensile strength of the sample is 6.1% and 11% higher than the estimated strength value of the empirical formula. The yield strength and tensile strength of the sample 1 were increased by 9.0% and 2.0% respectively before production, and those of the sample 2 were increased by 26.4% and 8.8% compared with before production).
(1) The geometric dimensions of large and small ends of stainless steel reducers are more accurate, but the wall thickness is very uneven. As for stainless steel reducers with straight sections, the wall thickness of the small end of the eccentric reducer is thicker than that of the large end, while the wall thickness of the small end of the concentric reducer is thinner than that of the large end. The wall thickness of the reducing elbow is more uniform. Therefore, the geometric dimensions of the large and small ends must be measured when they are tested.
(3) The ellipticity of the stainless steel reducer is less than 2%; the bending radius error of the reducing elbow is also small and can be ignored.
(4) The surface hardness of the two ends of the stainless steel reducer is about 35% lower than that of the middle section on average.
(5) After the final normalizing treatment, the yield strength and tensile strength of the stainless steel reducer made of large-diameter pipes by hot pressing are significantly improved.
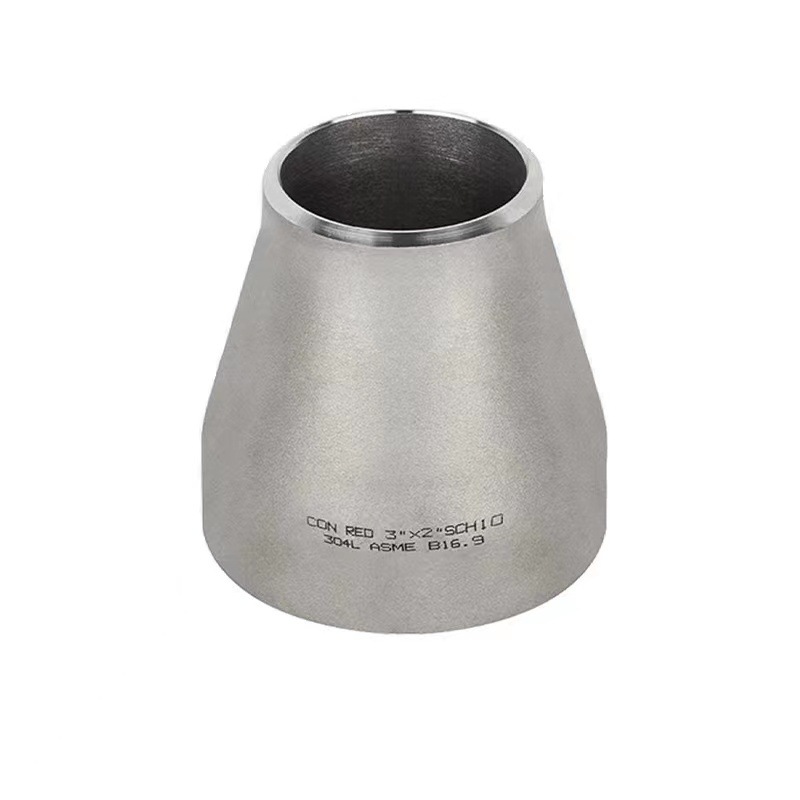